Article publié le 26 septembre 2014 sur 3D Natives
Fruit d’un partenariat entre la NASA et la société Made In Space, la Zero-G est la première imprimante 3D à être entré dans l’espace ce dimanche 21 septembre ! L’imprimante, qui fait partie du projet « 3D printing in Zero-G experiment » lancé en mai 2013, permettra de réaliser une série d’expérimentations d’impressions 3D en apesanteur sur les prochains mois.
Si les tests s’avèrent concluants, le projet pourrait permettre aux cosmonautes de fabriquer à la demande outils et pièces de rechange durant leur séjour au sein de la Station Spatiale Internationale (ISS). Un telle machine offrirait davantage d’indépendance vis à vis de la Terre, et pourrait devenir un élément clef dans la réussite de missions à plus long terme, et qui dit plus long dit aussi plus loin !

L’imprimante 3D Zero-G qui équipe la station spatiale internationale depuis dimanche dernier
Basée en Californie, la société Made In Space a été fondée en 2010 par Aaron Kemmer, Jason Dunn et Mike Chen, avec pour objectif de construire le futur de l’humanité dans l’espace. Une belle ambition donc, et une technologie qui pourra certainement accélérer le développement des activités spatiales.
Parallèlement, la NASA annonce avoir pour objectif de réduire ses coûts grâce à cette technologie, qui devrait également permettre de réduire le nombre de pièces de rechange transportées et éviter des allers-retours inutiles.
Made in Space souligne toutefois qu’il s’agit encore d’un « vol test », et que de nombreuses études en conditions réelles restent à mener. Plus de 400 vols paraboliques ont déjà été effectués sur Terre pour reproduire des conditions de micropeseanteur, soit environ 30,000 heures de tests. D’autres questions, comme la résistance de la machine ou le comportement des matériaux plastiques extrudés en environnement spatial, soulèvent de vrais challenges pour l’équipe de recherche.
Retour sur l’imprimante 3D Zero-G en vidéo :
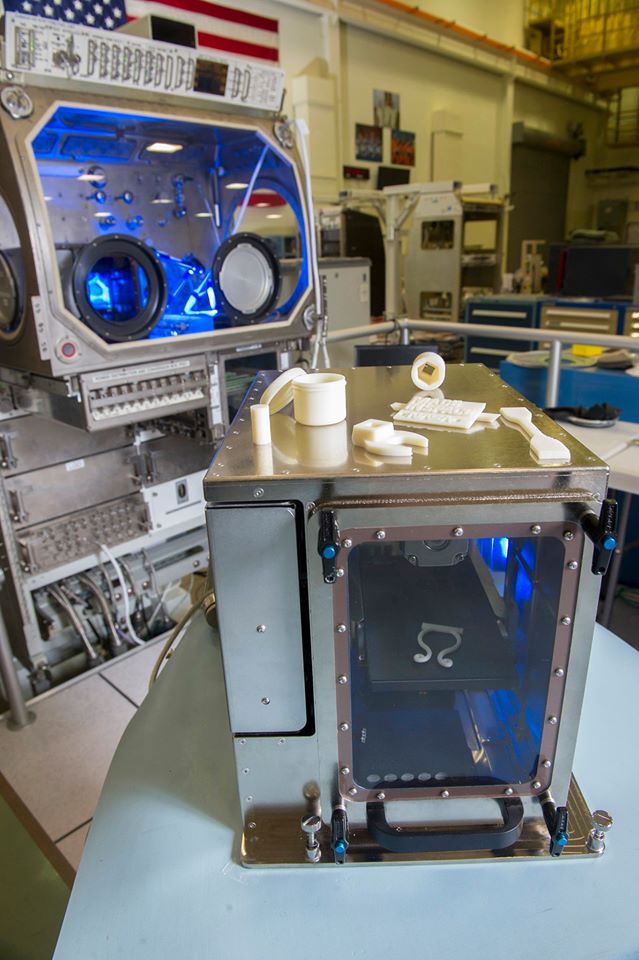
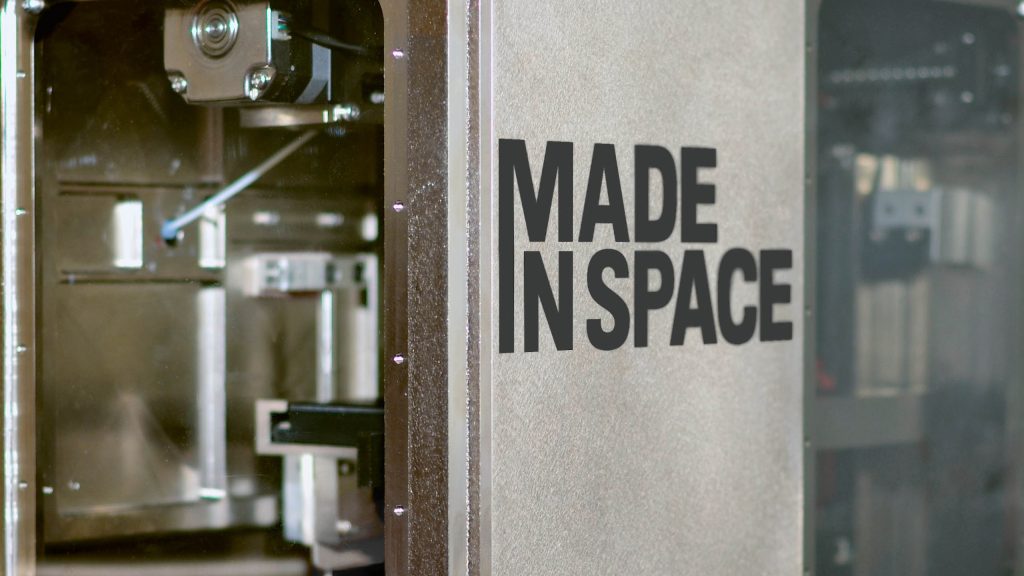
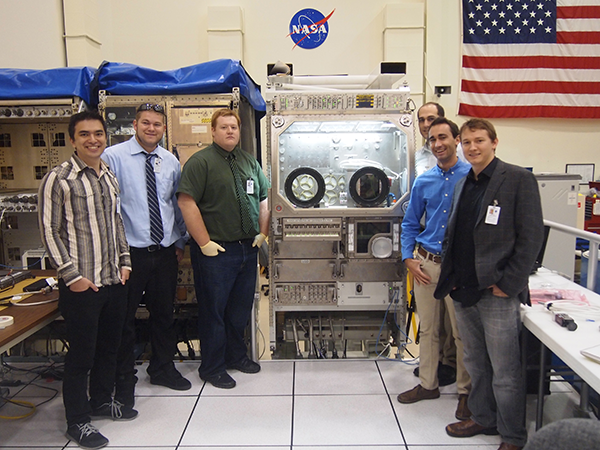